Will Smith – Director of Software, Adcole LLC
Was ist Chatter und seine Quellen
Rattermarken sind ein sich wiederholendes Muster kleiner Spitzen oder "Wellen", die in regelmäßigen Abständen auftreten und auf der fertigen Oberfläche eines bearbeiteten Werkstücks erscheinen können. Chatter ist kein Formfehler (Rundheit und Lappenbildung), und Rütteln ist kein Oberflächengüte (Rauheit); es liegt vielmehr zwischen diesen beiden Zuständen. Bei kritischen Bauteilen, wie z. B. einer rotierenden Welle in einem Motor, können Rattererscheinungen in der Endmontage zu Problemen führen, die einen vorzeitigen Ausfall des Bauteils zur Folge haben und andere Komponenten beschädigen können. Dieser Artikel befasst sich mit den Gründen für Rattererscheinungen in Wellenkomponenten, mit Bewertungsmethoden und mit den Ergebnissen von Messungen zur Verbesserung der Wellenqualität in hoch beanspruchten Baugruppen.
Rattergeräusche, eine der Hauptursachen für Geräusche, Vibrationen und Rauheit (NVH) in Motoren, lassen sich mit geeigneten Qualitätsverfahren und -geräten beseitigen. Rattergeräusche können bei allen Bearbeitungsvorgängen wie Fräsen, Drehen, Bohren, Schleifen usw. auftreten. Genauer gesagt, werden Rattergeräusche in der Regel durch Werkzeugunwuchten, mangelnde Steifigkeit der Werkzeuge oder Vorrichtungen, nicht-isotrope Teilesteifigkeit - ein besonderes Problem bei Kurbelwellen -, unrunde Teilezentren, schlecht funktionierende oder verschlissene Geräte und andere Unwucht- oder Vibrationsquellen verursacht.
Warum ist Chatter-Inspektion wichtig?
Modern motors and internal combustion engines (ICE) demand tighter tolerances and higher performance, making efficiency and longevity crucial. Rotating shafts with chatter patterns can cause excessive noise and vibration issues within the final assembly of an engine or motor, potentially leading to NVH concerns that could require recalls, which can lead to customer dissatisfaction, reputational damage, and loss of sales. This is particularly true in high RPM requirements such as EV rotor shafts, which can reach 20,000 RPM or more.
Chatter is a feature that has been measured and analyzed by manufacturers for decades, but is also overlooked when designing a new part. Whether for engines or motors, this parameter can be critical to monitor. While production machines are often prioritized in budgets, quality control equipment is equally important. Poor quality can be costly, so engineers and production managers must develop robust quality control systems and ensure they have the right equipment to measure necessary features.
Rattergeräusche treten häufig bei einer bestimmten Frequenz auf, die mit dem Verhältnis zwischen der Drehgeschwindigkeit der Schleifscheibe oder des Schneidwerkzeugs und der Drehzahl des Werkstücks zusammenhängt. Die sich daraus ergebende "Eigenfrequenz" des Prozesses weist eine gleichbleibende Signatur auf, wobei im Frequenzbereich oft höhere Oberwellen vorhanden sind. Die Prozessparameter werden angepasst, um die Amplitude bei dieser "Eigenfrequenz" zu kontrollieren und/oder die Frequenz, bei der sie auftritt, entsprechend den Produktanforderungen zu verschieben. Erhöhungen des Amplitudenwerts bei dieser Frequenz und/oder zusätzliche Amplitudenspitzen bei anderen Frequenzen weisen häufig auf ein prozessbezogenes Problem oder auf externe Einflüsse hin. Zu den äußeren Einflüssen können nahe gelegene Motoren, Pumpen, andere Geräte (wie Stanz- oder Pressmaschinen) oder Gabelstaplerverkehr gehören. Die Ratterausgabe kann Technikern und Ingenieuren dabei helfen, die Ursache des Problems zu finden, was zur Korrektur und Wiederherstellung der Produktqualität führt.
Wie man auf Chatter untersucht
Ausrüstung
Quality control machines are optimized to measure a specific set of parameters; for example, a precision tactile machine can often measure chatter, while an optical machine cannot (or not as effectively). Chatter is not something that would be detected by evaluating standard GD&T features like roundness or refinements of roundness data such as sector roundness or lobing. The amplitude can be quite small at sub-micron levels, the chatter may be limited to a single area, and the frequency of the chatter may vary significantly. However, regardless of the amplitude, region, or frequency variations, chatter can still have a discernible impact on the quality, final assembly, and performance of ICE or electric motors.
Eine tool for measuring chatter on shafts after a grinding process would be an Adcole tactile shaft metrology gage. These gages, along with proper software that can measure a wide range of GD&T parameters, provide valuable data and analysis to maintain the demanding quality required for rotating shafts. In the camshaft world, analysis of a lobe base circle region where the grinder velocity would be uniform over a constant radius provides a cleaner signal for detecting a chatter issue. The lift region of the lobe where radii rapidly changes could be analyzed separately, providing additional information over the surface that would have been ground with an adjustable velocity.
Bewertungsmethoden
"Da viele vibrationsbedingte Probleme bei bestimmten Frequenzen auftreten, kann die Ursache und der Ort der Vibration anhand von Amplitudenschwankungen bei bestimmten Frequenzen eingegrenzt oder identifiziert werden.” (Collins D., 2022) This is why calculating amplitude over a frequency domain is better than simply counting lobes or peaks within the profile error.
Alle Messdaten werden direkt in die Datenerfassungssoftware eingespeist, die das Signal entweder als Amplitude im Vergleich zur Zeit (als Zeitwellenform) oder als Amplitude im Vergleich zur Frequenz (als schnelle Fourier-Transformation (FFT)) oder beides aufzeichnet. All diese Daten werden von Computerprogramm-Algorithmen analysiert, die wiederum von Ingenieuren oder geschulten Schwingungsanalytikern ausgewertet werden, um den Zustand der Maschine zu bestimmen und mögliche bevorstehende Probleme wie Lockerheit, Unwucht, Ausrichtungsfehler, Schmierprobleme und vieles mehr zu erkennen. Die Schwingungsanalyse kann Probleme wie Radunwucht oder Radabrichtprobleme aufdecken.
Chatter can also mask itself on a shaft journal by showing up only over a small angular range. This makes it more difficult to measure and detect. Another method is the quadrant analysis option that can be used for journals on any rotating shaft. This allows for the entire 360 degrees of roundness data to be analyzed for chatter, and it breaks the roundness error into four 90-degree regions for chatter analysis. This analysis option provides a tool that can pick up a “chatter burst” on the surface of a journal where during the production process, a region of usually less than 90 degrees exhibits a pattern of undulations. The amplitude of these undulations is frequently too small to affect the roundness or even lobing measurement parameters, but can still cause issues with NVH in the final assembly of the engine. By analyzing the roundness error over 90 degrees, it is possible to measure a higher amplitude of chatter that may exceed the defined tolerance.
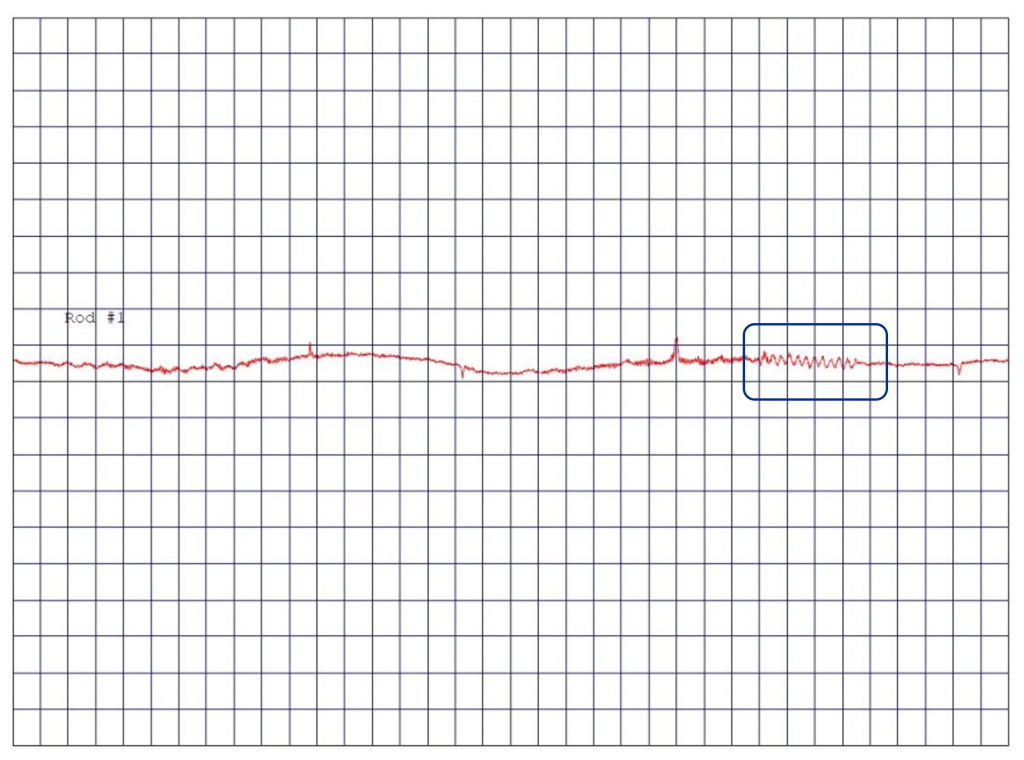
Eine Methode, um Chatter über einen begrenzten Winkelbereich zu finden, ist die "Schiebefenster"-Methode. Dabei kann das Winkelfenster in Grad und die Schrittweite des Schiebefensters eingestellt werden. Dieses gleitende Fenster durchläuft die gesamten 360 Grad der Rundheits- oder Profilfehlerdaten und bestimmt die maximale Amplitude und den Winkelbereich, in dem diese aufgetreten ist. Es ist auch wichtig, dass die erforderlichen Tests die Entwicklung einer Rattertoleranz und eines Ratterbereichs ermöglichen, der über einen bestimmten Winkelbereich analysiert werden kann. Dies kann durch die Durchführung einer Testreihe an bekannten "lauten" Wellen und den Vergleich mit der gleichen Testreihe an bekannten "leisen" Wellen erfolgen.
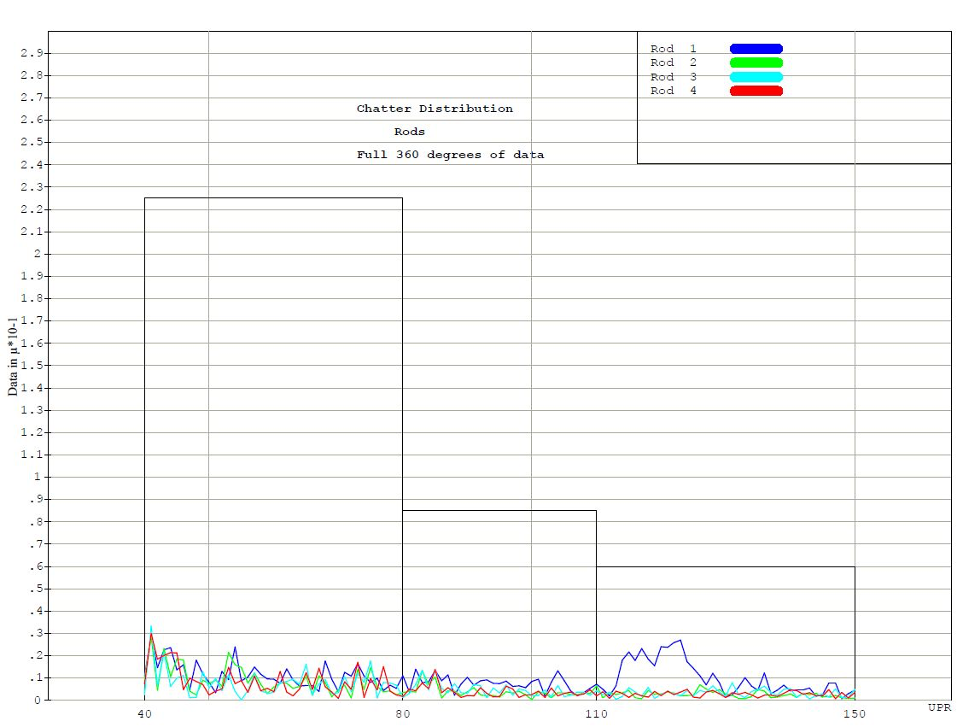
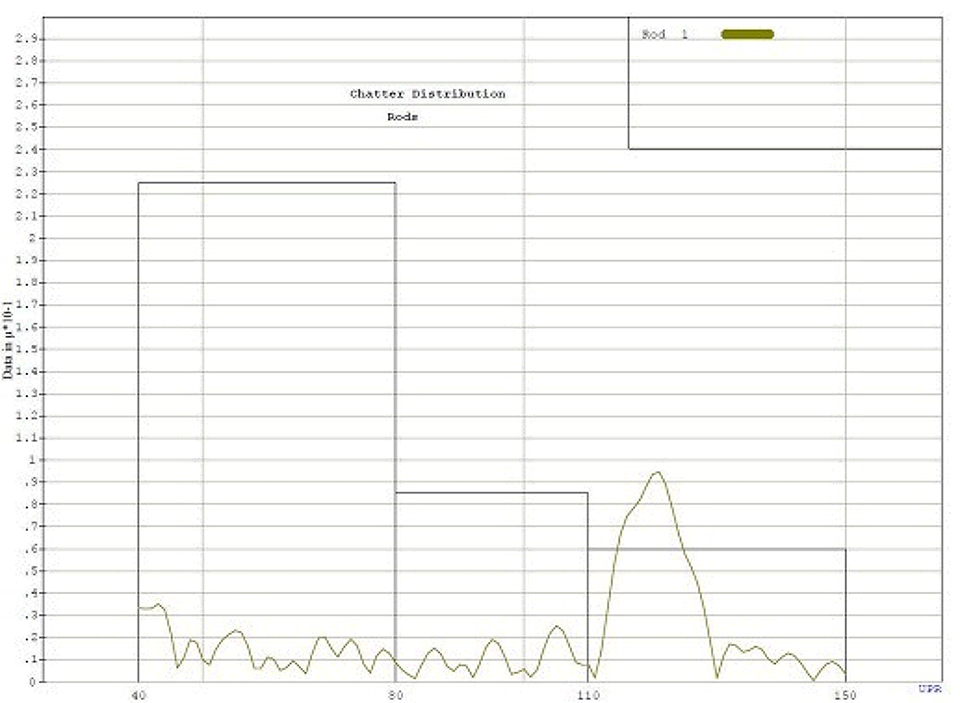
Ausgabe von Chatter-Messungen
Ratterer können auf der Oberfläche von Teilen auf unterschiedliche Weise auftreten. Manchmal kann es sich über ein großes Winkelfenster zeigen und eine saubere Frequenz haben. Dies kann in einer Rundheits- oder Profilfehlerkurve des zu messenden Elements sichtbar werden. Ratterer können jedoch auch in einem Rundheits- oder Profilfehlerdiagramm maskiert werden, da diese oft einen Filter auf die Fehlerdaten anwenden, der die Ratterer verbergen kann.
Unter Figure 2aIn diesem Abschnitt wird ein Fehlerdiagramm für die Rundheit des Zapfens und den Fehler des Nockenprofils der Nockenwelle dargestellt, wobei die sechs Nocken im unteren Teil des Diagramms zu sehen sind. Diese Nockenprofilgrafiken zeigen den Grundkreisbereich zwischen 0-90 Grad und 270-360 Grad. Der Fehler im Hubbereich liegt zwischen 90 und 270 Grad. In diesem Beispiel ist ein klares Muster von Wellen in der Grundkreisregion zu erkennen. Da der Grundkreis einen konstanten Radius hat, wird er normalerweise mit einer konstanten Geschwindigkeit geschliffen - dies gilt nicht für den Auftriebsbereich.
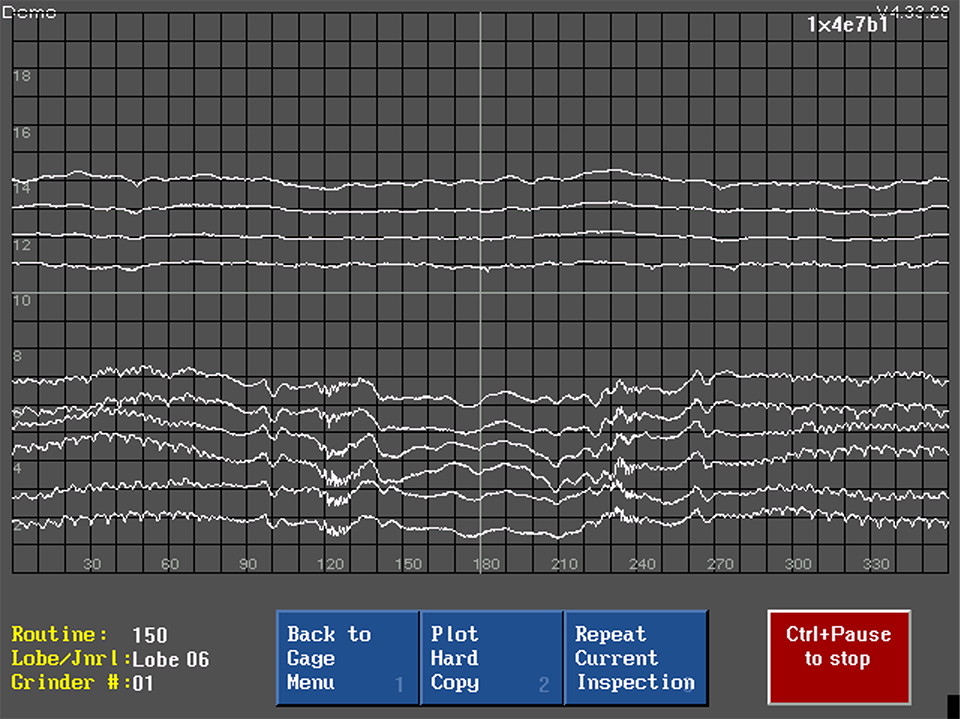
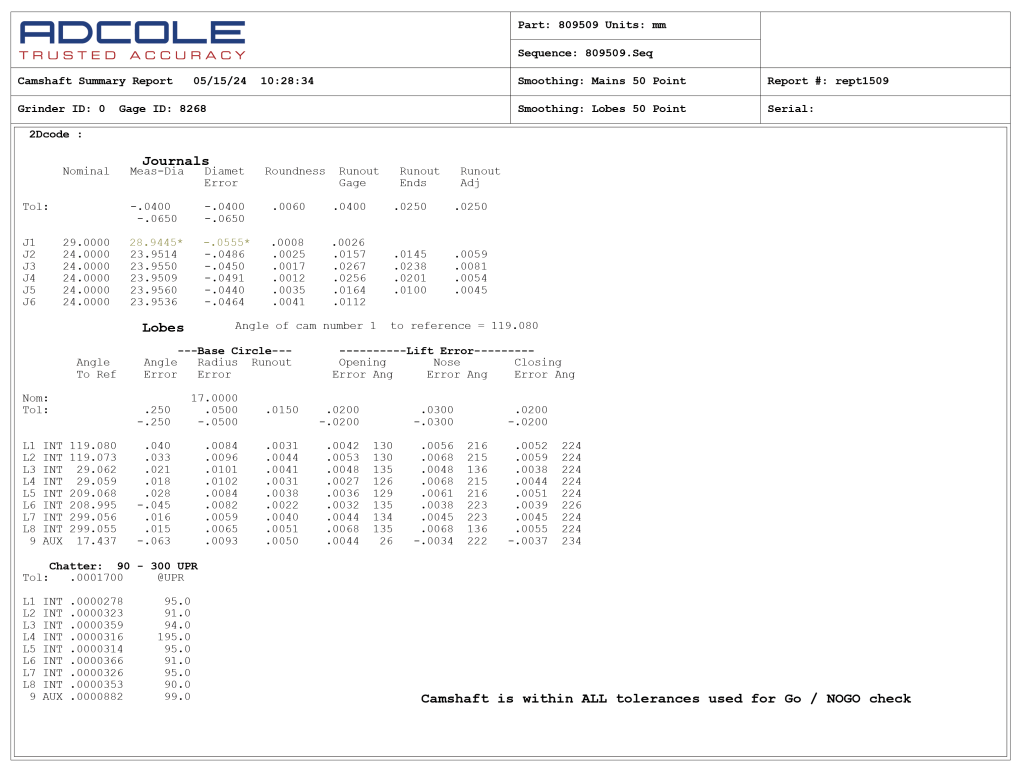
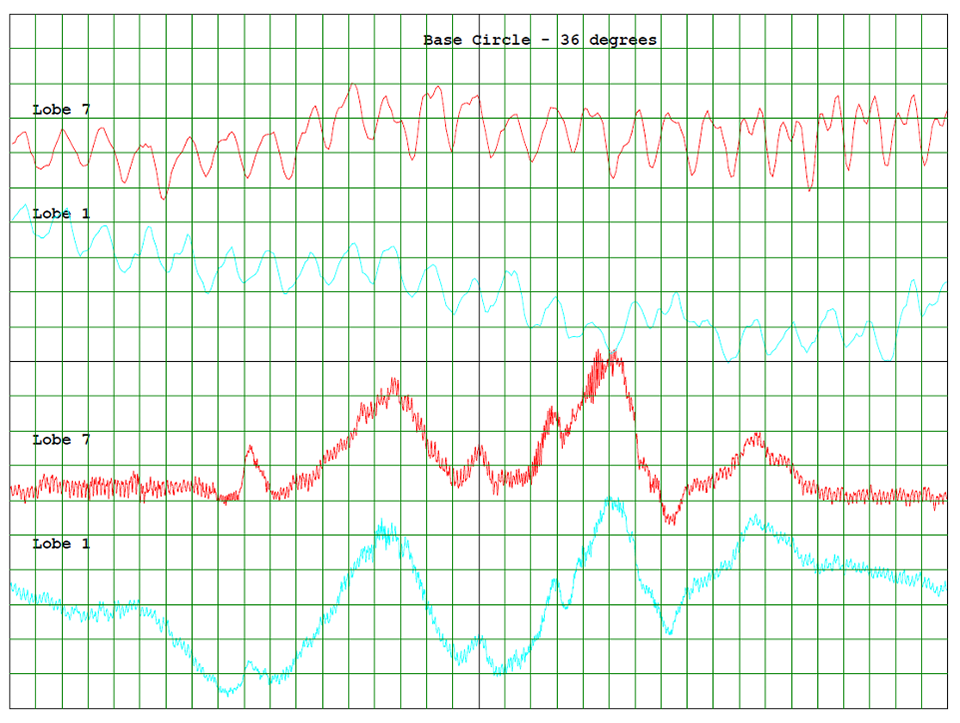
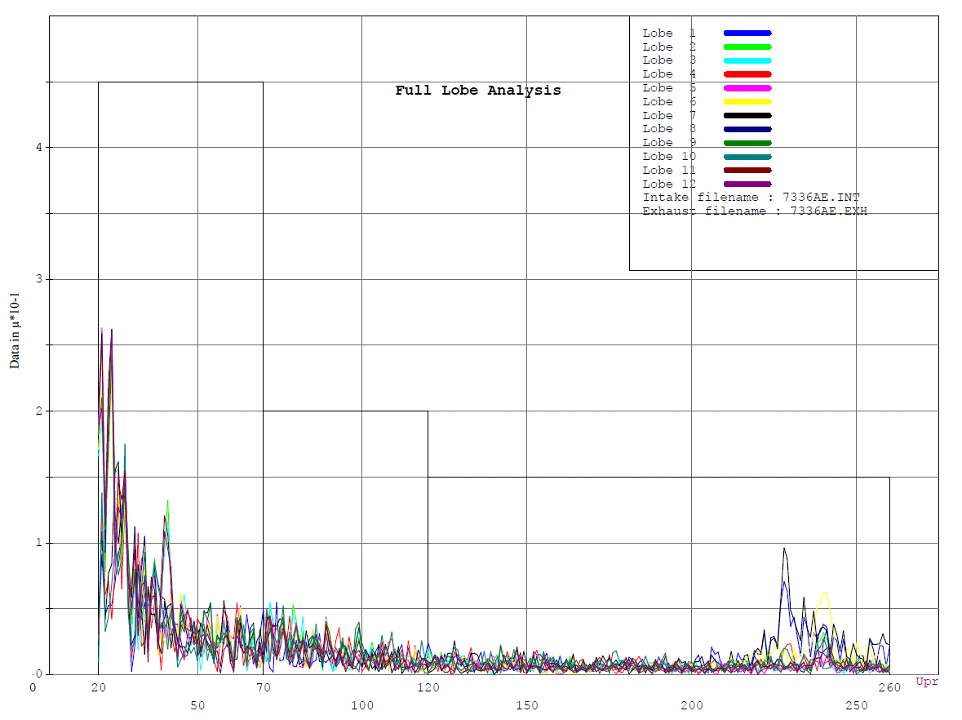
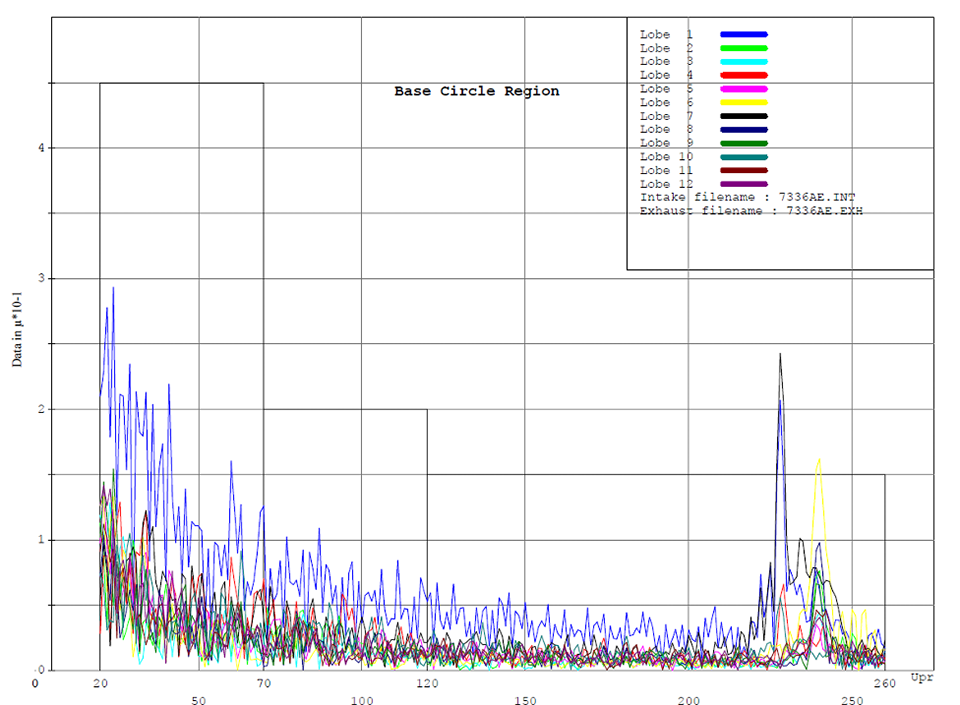
Einige Unternehmen verwenden ein Verfahren zum Zählen von Spitzen, um Probleme im Fertigungsprozess zu ermitteln. Dieses Verfahren ist nützlich, um Winkelbereiche in der Rundheit oder im Profilfehler zu bestimmen, die eine Nichtkonformität aufweisen, hat aber Schwächen, da es auf einer internen Definition beruht, wie eine Ausbuchtung oder Spitze definiert wird, damit sie gezählt werden kann. Dabei wird in der Regel nicht auf gleiche Abstände zwischen den Spitzen geachtet, so dass keine spezifische Häufigkeit des Auftretens bestimmt werden kann.
Schlussfolgerung
Die Messung von Rattern ist entscheidend für die konsistente Herstellung von Qualitätswellen, die über lange Zeiträume hinweg funktionieren, ohne Geräusche und Vibrationen zu verursachen, die zu einem schnelleren Verschleiß oder Ausfall des Teils führen können. Ein Präzisionsdrehteil mit messbarem Rütteln, das sich bei hohen Drehzahlen dreht, kann zu einem kompletten Motor- oder Systemausfall führen. Werkzeuge mit fortschrittlichen Analysemöglichkeiten, die Rattererscheinungen an der Oberfläche über definierte Bereiche hinweg untersuchen können, können ein Problem in der Fertigung erkennen, bevor das Produkt ausgeliefert wird. Wellenhersteller sollten die Investition in geeignete Qualitätswerkzeuge oder Lehren für Inline- oder Prüfraumeinstellungen einplanen, um potenzielle Fehler bei der Herstellung außerhalb der vorgegebenen Toleranzen zu analysieren und Maßnahmen zur Korrektur zu ergreifen.
Collins, D. (2022, October 17). How are fast Fourier transforms used in vibration analysis. Motion Control Tips. https://www.motioncontroltips.com/how-are-fast-fourier-transforms-used-in-vibration-analysis/